Presented by:
Editor’s note: This article appears in the new E&P newsletter. Subscribe to the E&P newsletter here.
Often an overshadowed element within the industry, solids management is estimated to impact more than 70% of fields globally. Defined as a well that requires solids handling equipment, solids management impacts the entire life cycle of a well. If left untreated, an accumulation of solids can lead to decreased production, reduced flow rates and the eventual shutdown of a well.
It is estimated that sand production accounts for almost 7% of total production losses, costing the industry millions of dollars each year.
Desanding technology has been around for decades and enables operators to remove sand and silt accumulations in the well. However, desanders typically have a large footprint, taking up valuable space on the rig floor and require additional personnel on board (POB).
Traditional solutions for managing solids in intervention, such as coiled tubing (CT), sidetracks, redrills or recompletions, do not offer a panacea of all ills. Instead, they can simply present new concerns including increased project costs and POB. The environmental impact of these solutions is also higher.
Compact solids removal system
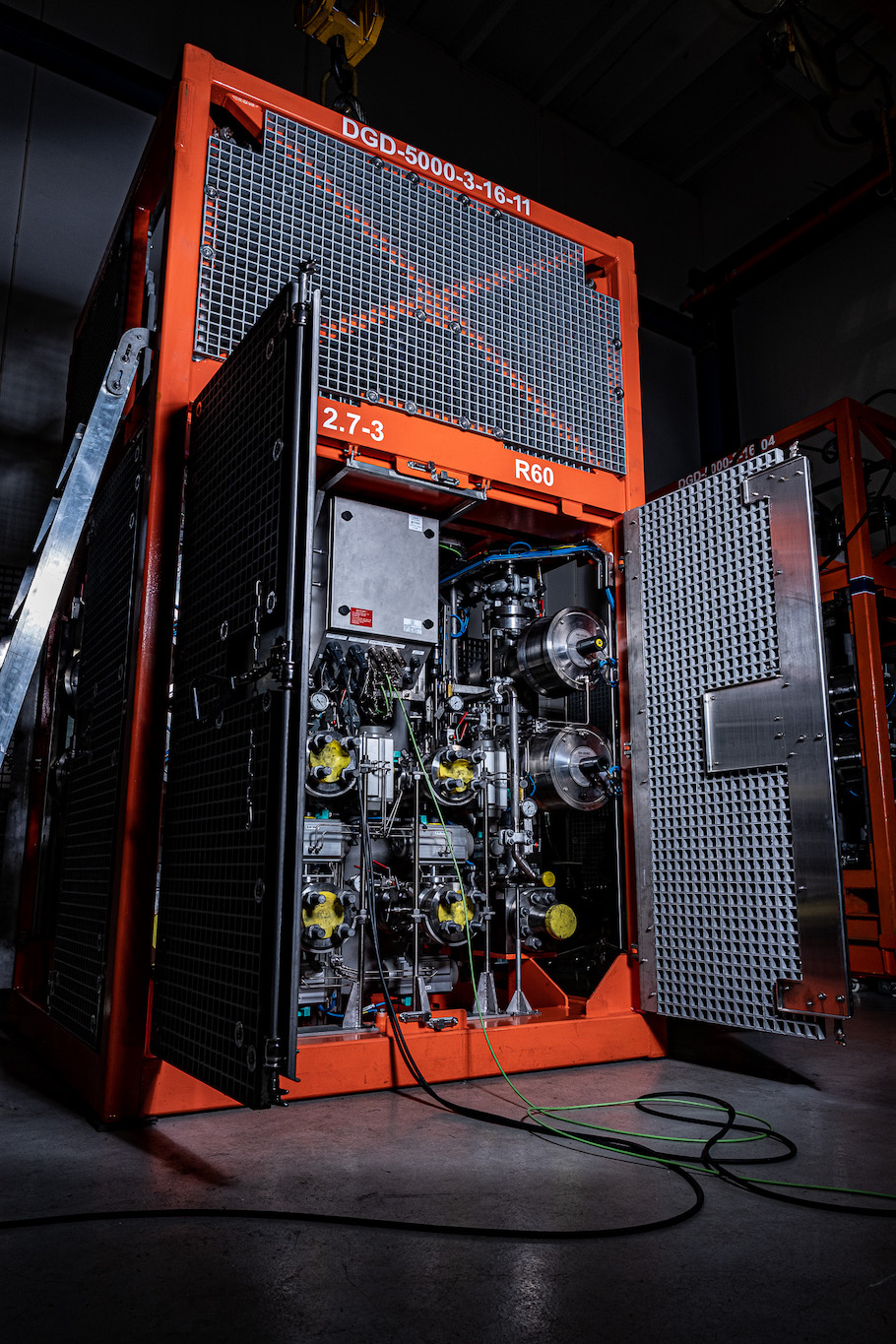
To minimize space on the crowded rig floor, engineers at FourPhase developed an advanced, compact solids removal system based on cyclone technology. Known as DualFlow, the technology is the only dual cyclone desander on the market with a 2×2-meter footprint. The smallest desander available, its modular design was strategically developed to create a flexible, stackable and compact solution. The technology weighs less than 10 t and requires minimal logistical impact.
Operationally supported by integrating 3D modeling and visualizations in the project planning phase, rigups are performed virtually, enabling specific elements to be detailed ahead of mobilization and saving valuable hours offshore.
The technology can be used at various points in the well life cycle across both production and intervention. This includes short flowbacks to get wells online, regular CT cleanout campaigns or the management of solids from an entire platform.
Solids management also has been brought into the digital age with the integration of more than 500 sensors to gather real-time solids data. By monitoring data, the system guarantees continuous production and fuels better decision-making.
This data-led approach facilitates increased production by monitoring and reducing the sand and solids concentration in the process facility. By improving solids management during production, it removes the need for expensive intervention operations caused by solids. Used continuously, the FourPhase system can provide an estimated value add of about $215 mNOK/year per well.
To date, DualFlow has delivered more than 50 operations for clients in eight markets for over 100,000 operational hours. Having recorded data across all operations since 2011, it is thought that FourPhase now has the biggest solids database in the world.
Moving to a data-led approach
DualFlow works by using single liner cyclonic technology. With two vessels contained in one desander, the design ensures continuous production. This works as one vessel can be isolated and flushed, while production continues through the other. With the ability to maintain a continuous flow rate, the system has a proven efficiency of 99.8%, with a dynamic range of 20 microns to 10-mm solids.
The DualFlow is aided by a control system that can perform advanced prediction simulations in real time. Operational ease of use is paramount to the technology’s design with only a PC required to operate.
It is the first automated solids management system with remote operation capabilities available on the market. The system delivers solids-free production flow while reducing operational costs and eliminating risks related to human error. The technology completely removes traditionally labor-intensive manual operations such as valve manipulation and flushing operations. These operations are now run automatically or with a click of a button locally, or remotely. Removal of such operations directly reduces POB and associated emissions.
Using machine learning algorithms, the operational solids database provides the new control system with predictive capabilities for managing well performance—bringing solids management into the smart, digital age.
Case study
The DualFlow desander has turned a $3.5 million CT campaign cost into a $58 million profit for a major Norwegian oil and gas producer in the North Sea. Following a screen collapse in a high-producing wellbore, a large volume of solids was produced; these subsequently reached the production facility. The well was immediately shut in due to solids handling limitations topside. A wireline operation was performed, and it was assumed that the well was almost filled with solids.
The well was scheduled for plug and abandonment (P&A). However, there was a requirement to clean the wellbore first, and a CT operation would be the typical solution in this situation.
Instead, the 5K DualFlow production enhancement system was installed as an intervention solution. The well was able to be kick-started, and most of the solids causing the blockage were extracted. The P&A operation was canceled, and the well was returned to production with an indication of high oil production potential.
The recovery of the well resulted in estimated earnings of $1.4 million during the initial recovery period. This equates to a $4.9 million increase over the total planned operation.
Now the well is being produced through the 5K DualFlow production enhancement system, providing an average oil production of about 560 standard cubic meters per day. The wellbore is maintained at surface with a separation efficiency of more than 99%. Total solids removed (YTD) equal 7,817 kg.
Due to the success of the DualFlow as an intervention and production solution, it is being rolled out across several wells belonging to the operator.
Green credentials
With data enabling greater visibility and analysis based on advanced prediction simulations, it is possible to change the standard approach to solids management. Rather than chocking back the well to restrict flow and reduce solids production, it is possible to increase production, utilizing desanders to effectively manage sand produced to the surface. This is particularly valuable in brownfield developments where increased water production typically results in higher sand production. Therefore, adopting desanders as a production solution can provide a strategic extension to the well life.
In addition, with the industry drive to be net zero by 2050, the DualFlow technology improves operators’ carbon footprint and helps operators reach their desired ESG goals. The separation and cleaning technology enables operators to remove and accurately log hydrocarbon contaminated sand particles. Data show that deploying this separation and cleaning technology on jetting operations can reduce the oil discharged to sea by up to 7%.
The reduced need for CT, and its associated intensive energy requirements and high-cost operations, further boost DualFlow’s green credentials. When compared with average CT activity, use of DualFlow reduces the required equipment weight from 160 t to 10 t—the logistical emissions are significantly reduced.
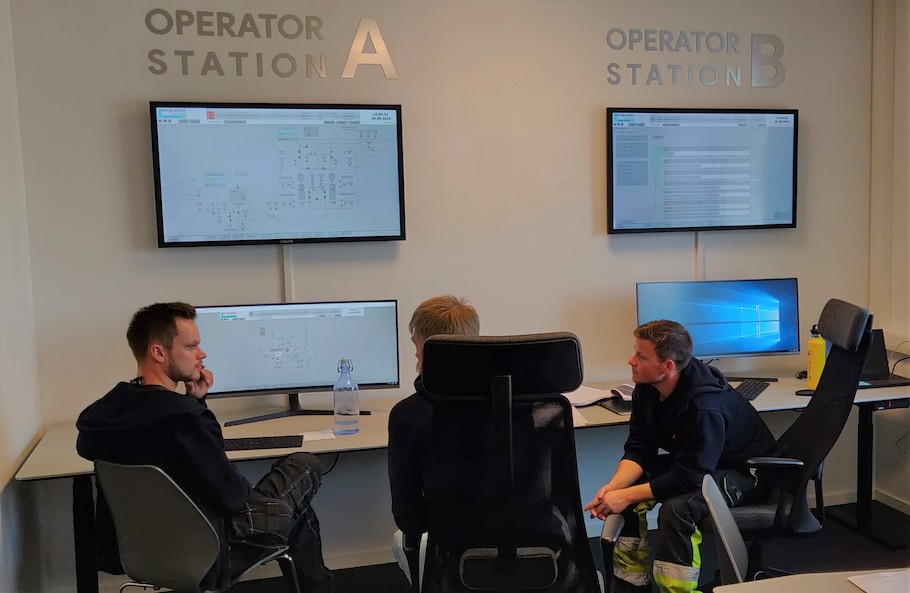
RELATED CONTENT:
April 21, 2021 FourPhase Delivers Production Optimization Project in North Sea
Feb. 10, 2021 Lessons from COVID-19: Prioritizing Oil Production Performance
2021 Class of E&P’s 40 Under Forty Technology Innovators
This post appeared first on Hart Energy.